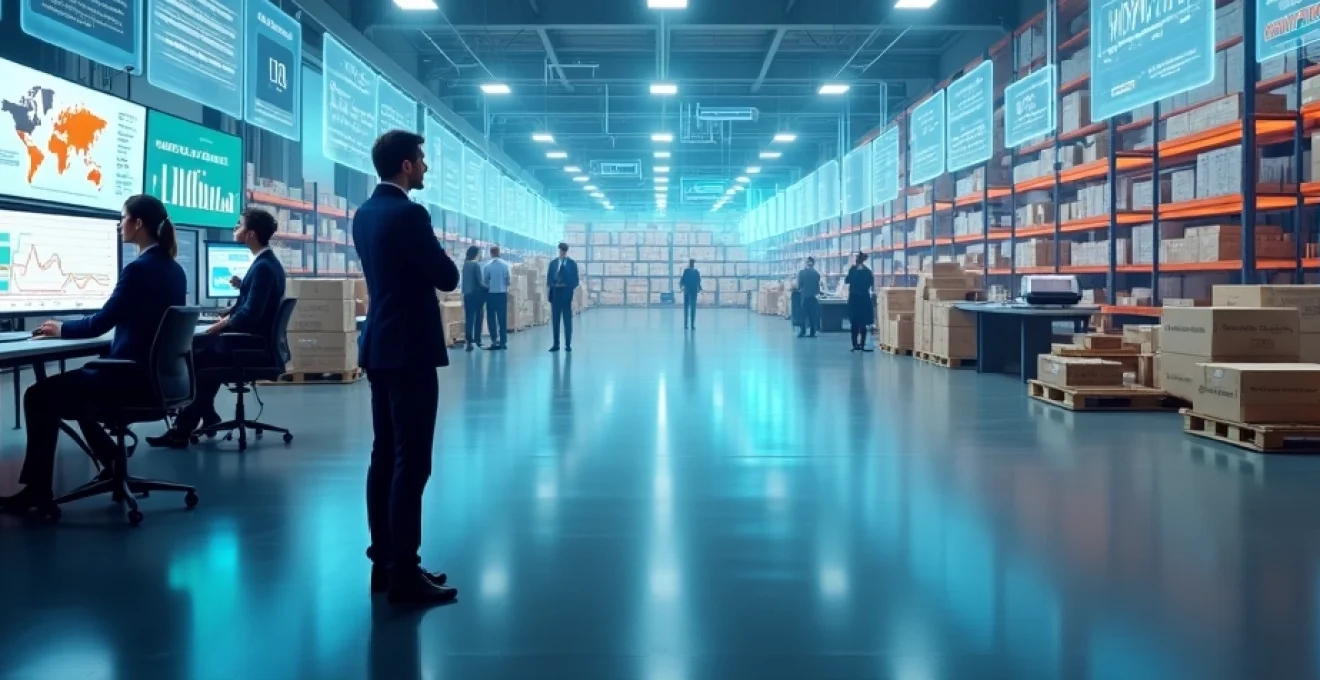
La gestion des approvisionnements représente un équilibre délicat au cœur de toute chaîne logistique performante. Trop de stock immobilise des capitaux et génère des coûts de stockage excessifs, tandis qu'un stock insuffisant provoque des ruptures qui impactent directement la satisfaction client et le chiffre d'affaires. Dans un contexte économique marqué par des fluctuations de la demande et des perturbations des chaînes d'approvisionnement mondiales, trouver le juste équilibre devient un enjeu stratégique majeur pour toute entreprise. Selon une étude récente de McKinsey, les entreprises qui excellent dans la gestion de leurs approvisionnements affichent une réduction de 15 à 30% de leurs coûts logistiques et une amélioration de 5 à 10% de leur niveau de service client.
La maîtrise des approvisionnements s'appuie sur des méthodes analytiques robustes, des stratégies éprouvées et des technologies adaptées. Elle nécessite également une approche différenciée selon les secteurs d'activité et les caractéristiques des produits. Face à la complexité grandissante des chaînes d'approvisionnement, les entreprises qui parviennent à anticiper la demande et à ajuster leurs stocks en conséquence bénéficient d'un avantage concurrentiel significatif. Plongeons dans les méthodes et outils les plus performants pour optimiser vos approvisionnements et naviguer avec agilité entre les écueils du surstock et des ruptures.
Diagnostic et prévision des flux d'approvisionnement
La première étape pour optimiser ses approvisionnements consiste à mettre en place un système fiable de prévision de la demande. Cette phase diagnostique repose sur l'analyse approfondie des données historiques de vente et la projection des tendances futures. Elle permet d'identifier les patterns de consommation, les variations saisonnières et les anomalies potentielles qui pourraient affecter les besoins en approvisionnement. Selon une étude d'Aberdeen Group, les entreprises dotées de systèmes de prévision avancés réduisent leurs stocks de 17% en moyenne tout en améliorant leur taux de service de 3 à 5%.
La qualité des prévisions dépend directement de la précision et de la pertinence des données analysées. Il est donc essentiel de disposer d'un historique fiable et d'outils analytiques performants. L'intégration de facteurs externes comme les tendances du marché, les actions marketing prévues ou les évolutions économiques permet d'affiner les prévisions et d'anticiper les variations de la demande. La combinaison de plusieurs méthodes prévisionnelles offre généralement les résultats les plus fiables, en compensant les faiblesses inhérentes à chaque approche par les forces des autres.
Méthodes quantitatives prévisionnelles (méthode Holt-Winters, régression linéaire, ARIMA)
Les méthodes quantitatives de prévision constituent la colonne vertébrale d'une gestion prévisionnelle efficace des approvisionnements. La méthode Holt-Winters, particulièrement adaptée aux séries temporelles avec tendance et saisonnalité, applique un triple lissage exponentiel qui prend en compte le niveau, la tendance et la composante saisonnière des données. Cette approche s'avère particulièrement efficace pour les produits dont la demande présente des variations saisonnières marquées, comme les produits de mode ou les articles liés aux saisons.
La régression linéaire, plus simple mais néanmoins puissante, établit une relation linéaire entre la demande et une ou plusieurs variables explicatives. Par exemple, la demande de certains produits peut être corrélée à des indicateurs économiques comme le PIB ou le pouvoir d'achat. Cette méthode est particulièrement utile lorsque vous disposez de données sur les facteurs pouvant influencer la demande future.
Le modèle ARIMA (AutoRegressive Integrated Moving Average) constitue une approche plus sophistiquée qui combine des composantes autorégressives et des moyennes mobiles. Particulièrement adapté aux séries temporelles complexes, ARIMA permet de capturer des patterns subtils dans les données historiques. Sa mise en œuvre requiert cependant une expertise statistique plus poussée et davantage de puissance de calcul, ce qui peut représenter un investissement significatif pour les PME.
La précision des prévisions quantitatives dépend davantage de la qualité des données d'entrée que de la sophistication du modèle utilisé. Un modèle simple alimenté par des données fiables surpassera toujours un modèle complexe basé sur des données approximatives.
Implémentation d'indicateurs clés de performance (KPI) pour la gestion des stocks
Pour piloter efficacement votre stratégie d'approvisionnement, il est indispensable de mettre en place un tableau de bord d'indicateurs pertinents. Le taux de rotation des stocks constitue un KPI fondamental qui mesure la vitesse à laquelle votre stock se renouvelle sur une période donnée. Un taux élevé indique une gestion efficiente, tandis qu'un taux faible peut signaler un surstock. La formule de calcul standard est : Taux de rotation = Coût des marchandises vendues / Stock moyen
.
Le taux de couverture, exprimé en jours ou en semaines, indique la durée pendant laquelle votre stock vous permet de satisfaire la demande sans réapprovisionnement. Ce KPI est particulièrement utile pour ajuster vos fréquences de commande. Sa formule est simplement l'inverse du taux de rotation, multipliée par la période considérée : Taux de couverture = (Stock moyen / Consommation moyenne) × Période
.
Le taux de service client mesure votre capacité à satisfaire immédiatement la demande des clients. Il se calcule comme le ratio entre les commandes intégralement satisfaites sans délai et le nombre total de commandes. Un objectif de 98% est généralement considéré comme excellent dans la plupart des secteurs, bien que certaines industries comme la pharmacie ou l'aéronautique visent des taux encore plus élevés.
D'autres KPI essentiels incluent le coût de possession du stock (qui comprend le stockage, l'assurance, l'obsolescence, etc.), le taux de rupture et le délai moyen d'approvisionnement. L'analyse croisée de ces indicateurs permet d'identifier les points d'amélioration prioritaires dans votre chaîne d'approvisionnement.
Analyse des données historiques avec le modèle ABC/XYZ
L'analyse ABC/XYZ constitue une méthode puissante pour segmenter votre portefeuille de produits selon deux dimensions cruciales. L'analyse ABC, basée sur le principe de Pareto, classe les articles selon leur valeur ou leur volume de ventes. Typiquement, les produits A représentent 80% de la valeur pour 20% des références, les produits B correspondent à 15% de la valeur pour 30% des références, et les produits C constituent 5% de la valeur pour 50% des références.
L'analyse XYZ, complémentaire à l'ABC, segmente les produits selon la prévisibilité de leur demande. Les produits X affichent une demande stable et hautement prévisible, les produits Y présentent des variations modérées avec une prévisibilité moyenne, tandis que les produits Z se caractérisent par une demande erratique et difficile à prévoir.
La combinaison des deux analyses génère une matrice à neuf segments (AX, AY, AZ, BX, etc.) qui permet d'adapter finement vos stratégies d'approvisionnement. Par exemple, les produits AX, à haute valeur et demande prévisible, sont candidats à des approches de flux tendus, tandis que les produits AZ nécessitent des stocks de sécurité plus importants malgré leur valeur élevée, en raison de leur volatilité.
Catégorie | X (Prévisible) | Y (Variable) | Z (Erratique) |
---|---|---|---|
A (Haute valeur) | Flux tendu, JIT | Stock minimal, révision fréquente | Stock de sécurité optimisé |
B (Valeur moyenne) | Approvisionnement régulier | Stock tampon modéré | Stock plus important |
C (Faible valeur) | Commandes groupées | Approvisionnement périodique | Stock max ou commande à la demande |
Utilisation du DRP (distribution requirements planning) pour anticiper les besoins
Le DRP (Distribution Requirements Planning) représente une extension logique du MRP (Material Requirements Planning) adaptée aux réseaux de distribution complexes. Cette méthode permet de synchroniser les approvisionnements à travers l'ensemble de votre réseau logistique, en prenant en compte les besoins de chaque entrepôt, centre de distribution ou point de vente. Le DRP détermine quand et combien commander pour chaque nœud du réseau, en fonction des prévisions de vente, des délais d'approvisionnement et des niveaux de stock existants.
L'implémentation d'un système DRP efficace nécessite une architecture informatique intégrée qui collecte et traite les données de tous les points de distribution. Les avantages incluent une réduction substantielle des niveaux de stock globaux, une meilleure rotation des produits, une diminution des ruptures et une optimisation des coûts logistiques. Selon une étude de Gartner, les entreprises qui déploient correctement le DRP réduisent leurs stocks de 20 à 30% tout en améliorant leur taux de service.
Pour maximiser l'efficacité du DRP, il est essentiel d'intégrer des paramètres comme les contraintes de capacité des entrepôts, les minimums de commande fournisseurs et les économies d'échelle liées aux volumes. La précision des prévisions de vente à chaque niveau du réseau constitue également un facteur critique de succès pour cette approche.
Stratégies avancées pour définir les niveaux de stock optimaux
La définition précise des niveaux de stock optimaux représente le cœur d'une politique d'approvisionnement efficace. Cette démarche vise à déterminer le point d'équilibre entre le coût de possession du stock et le coût des ruptures potentielles. Les stratégies avancées d'optimisation des stocks s'appuient sur des modèles mathématiques sophistiqués qui prennent en compte la variabilité de la demande, les contraintes opérationnelles et les objectifs de niveau de service.
L'approche scientifique de détermination des niveaux de stock repose sur l'analyse statistique des données historiques et la modélisation probabiliste des scénarios futurs. Elle permet de calculer avec précision les paramètres clés comme le stock de sécurité, le point de commande et la quantité économique de commande. Cette rigueur analytique transforme la gestion des stocks d'un art empirique en une science exacte, réduisant ainsi la part de subjectivité dans les décisions d'approvisionnement.
Calcul du stock de sécurité selon la formule de poisson et la loi normale
Le stock de sécurité constitue votre police d'assurance contre les aléas de la demande et des délais d'approvisionnement. Son calcul précis s'avère essentiel pour éviter à la fois les ruptures coûteuses et l'immobilisation excessive de capital. Deux approches statistiques principales permettent de déterminer le niveau optimal de stock de sécurité : la distribution de Poisson et la loi normale.
La distribution de Poisson s'applique particulièrement bien aux produits à faible rotation ou à demande intermittente. La formule simplifiée du stock de sécurité selon Poisson est : SS = k × √λ
, où λ représente la demande moyenne pendant le délai d'approvisionnement et k le facteur de sécurité correspondant au niveau de service cible. Cette approche est particulièrement adaptée aux pièces détachées ou aux produits spécialisés.
Pour les produits à rotation plus élevée et à demande continue, la loi normale offre un modèle plus approprié. La formule générale devient alors : SS = Z × σ × √L
, où Z représente le facteur de sécurité selon la table de la loi normale (1,65 pour un taux de service de 95%, 2,33 pour 99%), σ l'écart-type de la demande quotidienne, et L le délai d'approvisionnement en jours. Cette formule peut être affinée pour intégrer également la variabilité du délai d'approvisionnement.
L'efficacité de ces calculs dépend fortement de la qualité des données historiques et de la pertinence du modèle statistique choisi par rapport au comportement réel de la demande. Un monitoring régulier des performances permet d'ajuster les paramètres pour maintenir l'équilibre optimal entre protection contre les ruptures et minimisation des coûts de stock.
Mise en place du système kanban et des boucles d'approvisionnement
Le système Kanban, développé à l'origine par Toyota, représente une méthode visuelle et intuitive de gestion des flux d'approvisionnement basée sur la consommation réelle. Cette approche pull contraste avec les systèmes traditionnels de prévision en tirant les approvisionnements en fonction des besoins effectifs plutôt qu'en les poussant selon des prévisions. Le principe fondamental repose sur des signaux visuels (cartes Kanban) qui déclenchent le réapprovisionnement lorsqu'un niveau prédéfini est atteint.
Les boucles d'approvisionnement Kanban fonctionnent typiquement avec deux niveaux de déclenchement : le point de commande qui initie le réapprovisionnement et le niveau maximum qui définit la quantité à commander. La formule de base pour déterminer le nombre de cartes Kanban nécessaires est : N = (D × L × (1+α)) / Q
, où D représente la demande quotidienne, L le délai de réapprovisionnement, α le coefficient de sécurité, et Q la taille du conteneur standard.
L'implémentation d'un système Kanban efficace requiert une standardisation des contenants, une formation adéquate des équ
ipes, une définition claire des procédures et une mise en place progressive par zones. Les avantages incluent une réduction des stocks, une simplification des flux, une plus grande réactivité et une identification rapide des problèmes de qualité. Cette approche est particulièrement efficace pour les produits standard à demande régulière, mais moins adaptée aux produits à forte variation ou à demande erratique.
Bien que traditionnellement associé à des cartes physiques, le Kanban moderne s'est digitalisé avec des systèmes électroniques qui offrent une meilleure traçabilité et des analyses plus poussées. Des entreprises comme Bosch ou Amazon ont adapté cette méthodologie à leurs contextes spécifiques, créant des variantes comme le "e-Kanban" ou le "two-bin Kanban" pour optimiser davantage leurs flux logistiques.
Application de la méthode EOQ (economic order quantity) de wilson
La formule EOQ, également connue sous le nom de formule de Wilson, constitue l'une des approches les plus fondamentales pour déterminer la quantité optimale à commander. Développée en 1913, cette méthode mathématique reste pertinente en définissant le point d'équilibre entre les coûts de passation de commande et les coûts de possession du stock. La formule classique s'exprime ainsi : EOQ = √(2DS/H)
, où D représente la demande annuelle, S le coût fixe de passation d'une commande, et H le coût annuel de possession d'une unité en stock.
Cette approche permet d'équilibrer deux forces contradictoires : commander fréquemment en petites quantités réduit les coûts de stockage mais augmente les frais administratifs et logistiques, tandis que commander rarement en grandes quantités produit l'effet inverse. L'application rigoureuse de l'EOQ garantit la minimisation du coût total d'approvisionnement. Une étude de l'Université de Stanford démontre qu'une implémentation correcte de l'EOQ peut réduire les coûts logistiques totaux de 5 à 15%.
Malgré sa simplicité conceptuelle, l'EOQ repose sur plusieurs hypothèses qui peuvent limiter son application directe : une demande constante, des coûts stables, l'absence de ruptures de stock et un réapprovisionnement instantané. Des versions plus sophistiquées comme l'EOQ avec remises sur quantité ou l'EOQ avec ruptures planifiées permettent de s'adapter à des contextes plus complexes. Pour maximiser son efficacité, il est recommandé de recalculer périodiquement l'EOQ pour tenir compte des évolutions de la demande et des coûts.
Définition des points de commande (ROP) adaptés aux variations saisonnières
Le point de commande (Reorder Point ou ROP) détermine le niveau de stock qui, une fois atteint, déclenche automatiquement une nouvelle commande. Dans sa forme la plus simple, il se calcule comme la somme de la demande pendant le délai d'approvisionnement et du stock de sécurité : ROP = (Demande moyenne journalière × Délai d'approvisionnement) + Stock de sécurité
. Cette approche classique suppose toutefois une demande relativement stable, hypothèse rarement vérifiée pour les produits saisonniers.
Pour intégrer les variations saisonnières, les points de commande doivent être dynamiques et ajustés en fonction des périodes de l'année. Une méthode efficace consiste à calculer des indices saisonniers qui reflètent l'ampleur des variations par rapport à la moyenne annuelle. Ces indices, appliqués à la formule standard du ROP, permettent d'ajuster automatiquement les seuils de déclenchement en fonction des saisons. Par exemple, un produit dont la demande estivale est double de la moyenne annuelle verra son point de commande augmenté proportionnellement pendant cette période.
Les systèmes d'approvisionnement avancés intègrent des algorithmes qui recalculent automatiquement les points de commande en fonction des prévisions saisonnières actualisées. Cette approche proactive évite l'effet "coup de fouet" (bullwhip effect) qui amplifie les variations de la demande tout au long de la chaîne d'approvisionnement. Des entreprises comme Zara ou Uniqlo, confrontées à des cycles saisonniers marqués, ont développé des modèles sophistiqués de points de commande dynamiques qui leur permettent de maintenir des taux de service élevés tout en minimisant les stocks.
Technologies et logiciels de gestion des approvisionnements
Face à la complexité croissante des chaînes d'approvisionnement, les technologies digitales sont devenues indispensables pour gérer efficacement les flux logistiques. Les solutions informatiques modernes permettent d'automatiser les processus de commande, d'analyser en temps réel les niveaux de stock et d'anticiper les besoins futurs avec une précision croissante. L'investissement dans ces technologies constitue désormais un facteur clé de compétitivité pour les entreprises de toutes tailles.
L'écosystème des solutions logicielles dédiées à la gestion des approvisionnements s'est considérablement enrichi ces dernières années, offrant des options adaptées à tous les secteurs et à toutes les tailles d'organisation. Du simple module de gestion des stocks intégré à un ERP jusqu'aux plateformes spécialisées d'optimisation logistique basées sur l'intelligence artificielle, le choix d'une solution adaptée représente un enjeu stratégique. Les technologies émergentes comme le machine learning, la blockchain ou l'Internet des Objets (IoT) ouvrent de nouvelles perspectives pour une gestion encore plus précise et proactive des approvisionnements.
Comparatif des ERP spécialisés: SAP MM, oracle inventory, microsoft dynamics 365 SCM
Les solutions ERP constituent souvent le socle technologique de la gestion des approvisionnements pour les moyennes et grandes entreprises. SAP Materials Management (MM) s'impose comme la référence du marché avec une couverture fonctionnelle exceptionnelle, incluant la gestion des achats, le contrôle des factures, la gestion des stocks et la valorisation des inventaires. Sa richesse fonctionnelle s'accompagne toutefois d'une complexité significative et d'un coût d'implémentation élevé, le positionnant principalement sur le segment des grandes entreprises.
Oracle Inventory, composante de la suite Oracle SCM Cloud, se distingue par son architecture cloud native offrant une grande flexibilité de déploiement et une mise à jour continue. Ses points forts incluent des capacités analytiques avancées et une excellente intégration avec les autres modules Oracle. La solution propose des fonctionnalités de prévision basées sur le machine learning qui améliorent significativement la précision des approvisionnements, mais présente une courbe d'apprentissage relativement abrupte pour les utilisateurs.
Microsoft Dynamics 365 Supply Chain Management offre un compromis intéressant entre richesse fonctionnelle et facilité d'utilisation. Son interface intuitive, similaire aux autres produits Microsoft, réduit considérablement le temps de formation. La solution se distingue par ses capacités de planification avancée et d'optimisation des stocks en temps réel. Son intégration native avec Power BI permet de créer des tableaux de bord personnalisés offrant une visibilité accrue sur les performances de la chaîne d'approvisionnement. Le principal inconvénient reste la profondeur fonctionnelle légèrement inférieure à celle des leaders du marché pour certains cas d'usage spécifiques.
Le choix d'un ERP pour la gestion des approvisionnements doit s'inscrire dans une réflexion stratégique globale plutôt que dans une simple comparaison de fonctionnalités. La solution retenue doit s'aligner avec votre maturité organisationnelle, vos processus existants et vos objectifs de croissance.
Solutions WMS (warehouse management system) pour le suivi en temps réel
Les systèmes de gestion d'entrepôt (WMS) constituent la colonne vertébrale technologique d'une gestion optimisée des stocks physiques. Contrairement aux modules d'inventaire des ERP qui se concentrent sur les aspects financiers et transactionnels, les WMS orchestrent avec précision les mouvements physiques de marchandises au sein de l'entrepôt. Les solutions modernes comme Manhattan Associates, HighJump ou Mecalux Easy WMS permettent une traçabilité complète des produits depuis la réception jusqu'à l'expédition, optimisant chaque étape du processus.
L'apport majeur des WMS avancés réside dans leur capacité à opérer en temps réel grâce à l'utilisation de technologies comme la RFID, les codes-barres 2D ou les terminaux mobiles. Cette visibilité instantanée garantit une précision d'inventaire supérieure à 99%, contre 70-80% pour les méthodes manuelles traditionnelles. Les algorithmes d'optimisation intégrés déterminent automatiquement les emplacements de stockage optimaux en fonction des caractéristiques des produits et de leur vitesse de rotation, maximisant ainsi l'utilisation de l'espace disponible et réduisant les temps de préparation.
L'évolution récente des WMS vers des architectures cloud offre une flexibilité accrue et une réduction des coûts d'infrastructure. Des solutions comme Solochain de Generix Group ou Blue Yonder Warehouse Management intègrent désormais des capacités prédictives qui anticipent les goulets d'étranglement potentiels et proposent des ajustements proactifs. Ces fonctionnalités avancées permettent de réduire les délais de préparation de 30% en moyenne et d'optimiser l'allocation des ressources humaines et matérielles en fonction des pics d'activité prévus.
Implémentation de l'EDI (échange de données informatisé) avec les fournisseurs
L'EDI représente une technologie fondamentale pour fluidifier et sécuriser les échanges d'informations avec les partenaires commerciaux. En remplaçant les documents papier et les communications manuelles par des messages électroniques standardisés, l'EDI élimine les erreurs de saisie, accélère les cycles de commande et renforce la traçabilité des transactions. Selon une étude de GS1, l'implémentation de l'EDI réduit les coûts administratifs de 35% en moyenne et améliore la précision des données de plus de 40%.
Les documents les plus fréquemment échangés en EDI dans le contexte des approvisionnements incluent les commandes (ORDERS), les confirmations de commande (ORDRSP), les avis d'expédition (DESADV) et les factures (INVOIC). Des normes comme EDIFACT, ANSI X12 ou GS1 XML garantissent l'interopérabilité entre les systèmes hétérogènes des différents partenaires. Les plateformes EDI modernes comme IBM Sterling B2B Integrator, Generix EDI Services ou TrueCommerce offrent une gestion centralisée de ces flux et une intégration native avec les principaux ERP du marché.
L'évolution récente vers l'EDI collaboratif étend la portée au-delà des simples transactions pour englober le partage de données stratégiques comme les prévisions de vente, les niveaux de stock ou les indicateurs de performance. Cette approche, particulièrement pertinente dans le cadre de programmes VMI (Vendor Managed Inventory), permet aux fournisseurs d'anticiper vos besoins et d'optimiser leur propre chaîne d'approvisionnement. Les technologies API et les architectures microservices offrent désormais des alternatives plus agiles et moins coûteuses à l'EDI traditionnel, notamment pour les PME et les startups.
Outils d'analyse prédictive: tableau, power BI et solutions métier spécifiques
L'analyse prédictive transforme radicalement la gestion des approvisionnements en permettant d'anticiper les tendances futures plutôt que de simplement réagir aux événements passés. Des plateformes d'analyse comme Tableau et Power BI démocratisent l'accès à ces capacités prédictives grâce à des interfaces intuitives et des fonctionnalités de modélisation accessibles aux utilisateurs métier. Tableau excelle particulièrement dans la visualisation interactive des données et l'exploration intuitive des tendances, tandis que Power BI se distingue par son intégration native à l'écosystème Microsoft et ses capacités de modélisation avancées via le langage DAX.
Au-delà de ces outils généralistes, des solutions spécialisées comme Blue Ridge Supply Chain Planning, ToolsGroup ou O9 Solutions apportent des algorithmes spécifiquement optimisés pour les problématiques d'approvisionnement. Ces plateformes intègrent des modèles sophistiqués qui prennent en compte les saisonnalités, les lancements de produits, les promotions et même les facteurs externes comme la météo ou les tendances économiques. Leur capacité à traiter simultanément des millions de combinaisons produit-localisation-période permet d'optimiser finement les approvisionnements à un niveau de granularité inatteignable manuellement.
L'émergence du machine learning et de l'intelligence artificielle amplifie encore le potentiel de ces outils prédictifs. Des algorithmes comme XGBoost, Random Forest ou les réseaux de neurones profonds identifient des patterns complexes dans les données historiques et améliorent continuellement leur précision au fil des cycles d'apprentissage. Des études de cas chez des détaillants comme Otto Group ou Zalando démontrent des réductions de stocks de 20% et des améliorations du taux de service de 5% grâce à ces approches avancées. L'accessibilité croissante de ces technologies via des services cloud comme Azure ML ou Amazon SageMaker les rend désormais envisageables même pour des entreprises de taille moyenne.
Collaboration fournisseurs et approche VMI (vendor managed inventory)
La collaboration avec les fournisseurs représente un levier stratégique majeur pour optimiser les approvisionnements au-delà des frontières de l'entreprise. En partageant des informations critiques comme les prévisions de vente, les niveaux de stock et les plannings de production, les partenaires de la chaîne logistique peuvent coordonner leurs activités plus efficacement et réduire les inefficiences structurelles. Selon une étude de McKinsey, les programmes de collaboration avancée peuvent réduire les niveaux de stock de 10 à 30% tout en améliorant la disponibilité des produits de 5 à 15%.
Le VMI (Vendor Managed Inventory) constitue l'une des formes les plus abouties de cette collaboration. Dans ce modèle, le fournisseur assume la responsabilité de gérer les stocks de ses produits chez son client, en définissant lui-même les quantités et les moments de réapprovisionnement. Cette inversion du flux décisionnel traditionnel permet de réduire significativement l'effet "coup de fouet" qui amplifie les variations de la demande le long de la chaîne d'approvisionnement.